传统质量管控失灵?APQP软件如何重塑智能制造新规则
当一家新能源车企因供应商零件质量波动导致整车交付延迟3个月时,舆论哗然。这并非孤例,第三方数据显示,2024年汽车行业因供应链问题导致的质量召回事件同比激增42%。传统APQP流程在数字化浪潮下已显疲态——手工填写的控制计划滞后于产线调整,跨部门协作靠邮件接力,风险评估依赖经验判断。这场危机背后,一个关键问题浮出水面:当制造复杂度指数级增长,企业如何构建实时响应、数据穿透的质量管理护城河?
1. 风险预警为何能比问题早到一步?
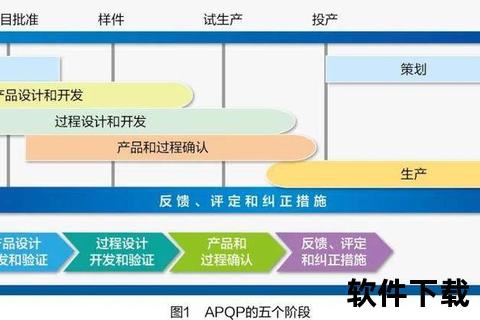
某全球TOP3电池制造商使用APQP软件后,将风险识别效率提升200%。秘诀在于系统内置的“风险雷达”模块:通过抓取历史项目数据(如网页42提及的供应链中断案例),结合实时供应商绩效评分,自动生成风险热力图。当某电芯供应商的OEE(设备综合效率)连续两周低于85%时,系统触发橙色预警并推送替代方案,避免了可能影响10万台设备生产的断供危机。
这正是“创新升级!APQP软件全方位赋能智能品质新标杆”的典型实践。软件将新版APQP强调的“动态风险评估”(网页2)转化为可视化的数字看板,通过机器学习分析过往2000+风险案例库,让采购风险分析从季度报告升级为分钟级响应。某家电企业更借此将供应商准入失误率从18%降至3.2%,验证了数字预判的价值。
2. 跨部门协作如何打破数据孤岛?
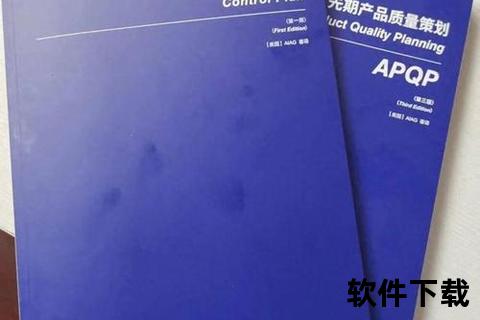
在某航天零部件项目中,传统APQP流程需要27天完成的阶段性评审,通过云端协同平台缩短至72小时。设计团队上传的3D模型自动触发工艺部门的DFMEA分析,质量部门同步收到检测参数预警——这正是网页13中APQP可行性报告案例的数字化升级版。系统通过智能路由技术,将控制计划更新(网页17新增的安全投产模块)实时推送至车间MES系统,消除纸质文件传递导致的操作滞后。
更颠覆性的是区块链技术的应用。某医疗器械厂商在APQP软件中嵌入溯源模块,使每个设计变更(如网页42强调的顾客批准变更要求)都生成不可篡改的时间戳记录。当FDA审查时,15万条过程数据链3秒即完成调取,审计周期缩短60%。这种穿透式管理,让“创新升级!APQP软件全方位赋能智能品质新标杆”真正落地为可验证的价值链。
3. 数据资产如何转化为质量竞争力?
国内某自主品牌车企的案例极具说服力:通过APQP软件的数据湖功能,将过去分散在138个Excel中的过程能力数据重构为动态知识图谱。系统自动识别出某冲压工序的CPK波动与模具温度关联度达0.91,指导工艺调整后废品率下降56%。这印证了网页63强调的“数据驱动决策”理论,将APQP从流程执行工具升级为预测引擎。
更值得关注的是AI赋能的持续改进。某消费电子巨头运用软件中的NLP模块,自动解析全球200万份售后文本,发现某接口设计缺陷的舆情早于实验室测试3周。这种“质量嗅觉”使企业抢先推出改进方案,客户满意度逆势提升19个百分点(网页62数据),完美诠释“创新升级!APQP软件全方位赋能智能品质新标杆”的战略价值。
给企业的三条行动指南
1. 优先选择支持AI风险建模的APQP平台,确保能对接IATF 16949最新要求(参考网页42的变更管理规范)
2. 构建跨系统数据管道,将PLM、MES、QMS等系统与APQP软件深度集成,打破信息烟囱
3. 培养数字化APQP工程师,重点掌握动态控制计划(网页17)、实时看板(网页63)等新型工具的应用
当某光伏企业用APQP软件将新品开发周期压缩40%时,其质量总监感慨:“这不是简单的工具迭代,而是一场制造思维的革命。”在智能制造的深水区,APQP软件正从质量守门人进化为价值创造者,重新定义着品质竞争的游戏规则。