创新智能公差分析软件:精准驱动高效工程决策新维度
在制造业高速发展的今天,一个看似微小却影响深远的问题正困扰着工程师:如何用有限的成本实现“零缺陷”生产?传统公差分析依赖人工经验和静态公式,常因计算误差导致设计返工、成本激增甚至产品失效。而随着市场竞争加剧,企业对精度与效率的需求愈发矛盾——既要求公差设计“严丝合缝”,又希望研发周期“快人一步”。这种矛盾背后,是传统方法的局限性与智能化浪潮的碰撞。
一、为什么说公差分析决定产品成败?
公差分析看似只是设计中的一环,实则贯穿产品全生命周期。以某国产新能源汽车品牌为例,其早期车型因车门装配间隙不均导致风噪问题,返工成本高达数百万。引入创新智能公差分析软件:精准驱动高效工程决策新维度后,团队通过DTAS 3D的蒙特卡洛仿真,在虚拟环境中模拟了200万次装配场景,发现密封条公差与钣金件形变的耦合效应是主因。优化后,车门装配合格率从82%提升至98%,研发周期缩短40%。
这类工具的核心优势在于“动态预测”。例如,3DCS软件在航空航天领域通过几何因子分析(Geofactor),识别出某卫星支架的安装角度公差对整体结构稳定性的敏感度,将关键尺寸公差从±0.1mm放宽至±0.15mm,单件成本降低12%。数据表明,采用智能公差分析的企业,产品不良率平均下降35%,研发成本减少20%。
二、智能算法如何突破传统分析瓶颈?
传统公差分析常受限于“一维计算”和“静态假设”,而创新智能公差分析软件:精准驱动高效工程决策新维度通过三大技术革新破解难题:
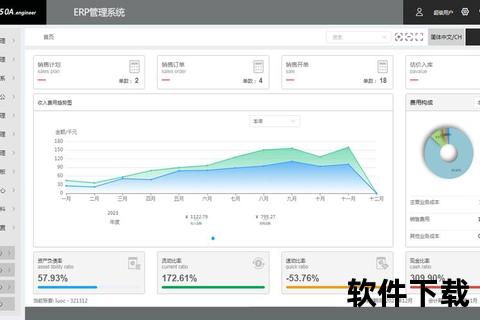
1. 多维度耦合建模
CETOL软件在洗衣机滚筒开发中,将轴承的圆度公差、皮带张力波动与电机转速动态关联,构建非线性方程求解。结果显示,仅调整皮带轮安装位置公差方向,即可减少63%的振动超标风险。
2. AI驱动的自动化迭代
某医疗器械企业使用DTAS 3D的AI建模功能,针对骨科植入物的2000多个装配节点,自动生成公差链并识别出贡献率超70%的5个关键尺寸,优化效率提升8倍。
3. 实时数据闭环
美的集团借助CETOL与CAD的深度集成,在设计阶段实时反馈公差对洗碗机门缝间隙的影响,避免后期模具修改,单项目节约成本超50万元。
三、从“试错”到“预判”,如何重构决策逻辑?
在精密制造领域,公差分析正从“事后验证”转向“正向设计”。以某光刻机零部件供应商为例,其采用Enventive软件进行3D公差叠加分析,提前预测晶圆台热膨胀与运动精度的关联性,通过调整材料匹配方案,将设备重复定位精度从±3nm优化至±1.5nm,达到国际领先水平。
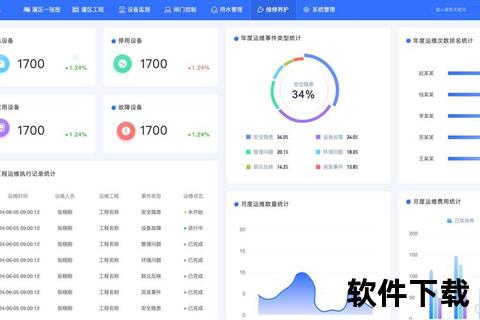
更值得关注的是数据驱动的决策模式。青山工业在差速器研发中,利用CETOL的敏感度分析功能,量化齿轮啮合面粗糙度与轴系跳动的交互影响,建立“公差-成本-性能”三维矩阵,实现从“经验决策”到“参数寻优”的跨越。此类工具使企业能够动态平衡质量与成本,例如某军工企业通过VSA软件的非刚性分析,在保证导弹尾翼装配精度的前提下,将铝合金框架的加工精度等级从IT6放宽至IT7,材料损耗减少18%。
行动指南:迈向精准制造的三步策略
1. 需求匹配:汽车/航空航天企业优先选择3DCS、CETOL等支持复杂装配的软件;中小制造企业可尝试GEOMATE或DCC等轻量化工具。
2. 技术融合:将公差分析软件与PLM、MES系统打通,例如Sigmetrix用户通过CETOL与Maple Flow的集成,实现公差数据与工艺参数的实时交互。
3. 人才培育:建立“专家模板库+工程师应用”的双层架构,如某企业通过DTAS 3D的模板化分析,使非专业人员在1分钟内完成80%的常规分析任务。
创新智能公差分析软件:精准驱动高效工程决策新维度,正在重塑制造业的底层逻辑。它不仅是工具升级,更是一场从“经验依赖”到“数据赋能”的认知革命。当公差设计从“模糊艺术”变为“精准科学”,中国制造向高端跃迁的路径也将愈发清晰。