当传统注塑工艺遇上智能技术:一场效率与成本的博弈
在塑料制品行业中,一个长期争议的话题始终存在:依赖老师傅经验的传统注塑工艺,是否会被智能技术彻底颠覆?过去,模具设计需要反复试模调整,缺陷预测全凭“手感”,工艺优化耗时数月,甚至可能因一个参数误差导致整批产品报废。随着“智能模流分析软件高效驱动注塑工艺精准优化新纪元”的到来,这场博弈的天平正悄然倾斜——数据显示,采用智能模流技术后,企业试模成本降低50%以上,产品缺陷率下降70%。这背后,是算法与工业场景的深度碰撞,更是传统制造业向数字化跃迁的缩影。
一、传统工艺痛点:如何用算法打破经验壁垒?
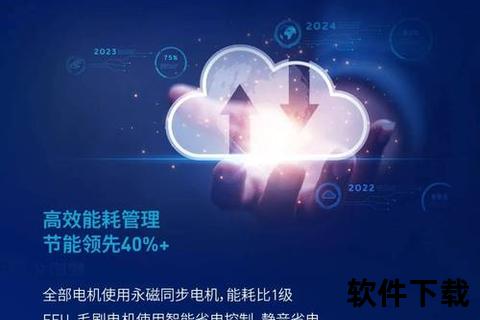
某汽车零部件企业曾面临这样的困境:一款复杂结构的仪表盘外壳在试模阶段频繁出现“短射”缺陷,工程师耗费3个月调整参数仍无果。引入智能模流分析软件后,系统仅用48小时便定位问题根源——浇口位置不合理导致熔体流动不平衡。通过模拟优化浇口布局和注射速度,最终实现了一次性试模成功。
案例支撑:
浙江某家电企业生产空调导风板时,传统工艺下产品变形率达15%。软件模拟显示,冷却系统布局不均导致局部应力集中。重新设计水路后,变形率降至3%,良品率提升直接带来年收益增加800万元。
此类案例印证:智能模流软件通过流体力学仿真,将注塑过程的“黑箱”可视化。它不仅能预测熔体流动路径(图1),还能量化压力、温度等关键参数,让经验不足的工程师也能快速掌握工艺优化的科学依据。
二、缺陷预测难题:怎样实现从“救火”到“防火”?
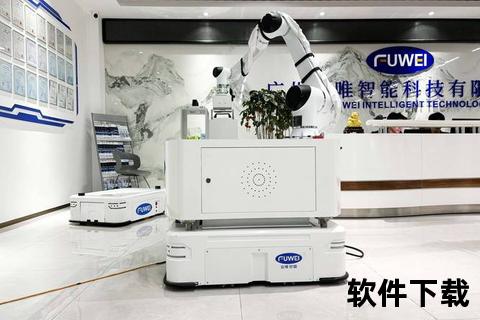
注塑件常见的熔接痕、气孔等缺陷,过去往往在量产阶段才暴露。某医疗器械企业生产的胰岛素笔外壳曾因内部微气泡导致强度不达标,整批产品召回损失超200万元。而智能模流软件通过“缺陷热力图”(图2),提前标记出高风险区域,指导调整保压压力和冷却速率,使气泡问题从根源消除。
数据验证:
在笔记本电脑外壳生产中,某企业通过软件模拟发现顶针位置设计不当会导致表面缩痕。优化后,产品外观不良率从12%降至1.5%,客户投诉减少90%。这种从被动修复到主动预防的转变,正是智能模流分析软件高效驱动注塑工艺精准优化新纪元的核心价值。
三、跨领域协同:为何说数据是新的生产资料?
当某新能源车企开发轻量化电池壳体时,面临材料(碳纤维增强塑料)、结构(薄壁蜂窝设计)、工艺(高速注塑)的多重挑战。传统模式下,材料供应商、模具厂、注塑车间需要反复沟通,耗时长达半年。而借助智能模流软件的协同平台,三方直接调用同一组数据模型:
材料供应商输入流变特性曲线
模具厂验证冷却系统效率
注塑车间模拟工艺参数组合
最终开发周期缩短至45天,材料损耗减少40%。
深层逻辑:
软件构建的数字化双胞胎(Digital Twin),打通了从材料科学到生产制造的“数据孤岛”。例如,针对PA66-GF30材料,系统可自动匹配最佳熔体温度(280-300℃)和保压时间(8-10秒),避免人工试错。这种基于数据的协同,正在重构制造业的价值链。
未来工厂的行动路线图
对于企业而言,拥抱智能模流分析软件高效驱动注塑工艺精准优化新纪元,需分三步走:
1. 能力筑基:优先在试模成本高、结构复杂的产线部署软件,通过典型案例积累数据资产(如某企业建立包含500种材料参数的数据库)。
2. 人机协同:培养既懂工艺又懂算法的复合型工程师,例如学习Moldflow高级分析技术(参考《Moldflow 2021模流分析从入门到精通》)。
3. 生态延伸:与高校共建仿真实验室,开发行业专用模块(如针对医疗产品的无菌成型模拟)。
这场变革的本质,不是机器取代人类,而是让工程师从重复劳动中解放,专注于创造性优化。当注塑机的轰鸣声与服务器的计算声共振,制造业的下一轮生产力革命已然拉开帷幕。