一、算法真的能取代人工经验?
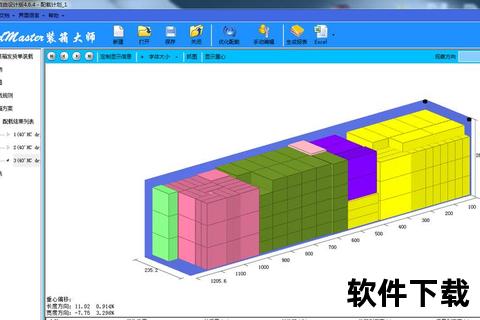
传统物流行业长期依赖“老师傅”的经验来规划装箱方案,但人工计算效率低、误差大,货物形状差异导致的“空隙浪费”普遍存在。以某电商企业为例,其人工规划的平均装载率仅为78%,每年因空间浪费产生的额外运输成本高达120万元。
高效能智能集装箱装箱计算软件轻松优化空间利用率新体验的核心突破在于算法优化。例如“悠闲装箱”通过混合整数规划与深度学习技术,对货物尺寸、重量、堆叠限制等参数进行多维度分析,生成3D装载模型。其算法支持全隔板、混装、旋转等12种装箱模式,并自动规避重心偏移风险。某化工企业使用后,40尺高柜装载率从82%提升至95%,单箱运输成本下降18%。
更值得关注的是动态调整能力。当某国际物流公司遭遇航线临时变更时,软件在15分钟内重新生成适配新港口装卸设备的方案,避免因设备高度限制导致的30%空间浪费。这种“决策-反馈-优化”的闭环机制,正是人工经验难以企及的。
二、动态调整能否应对突发需求?
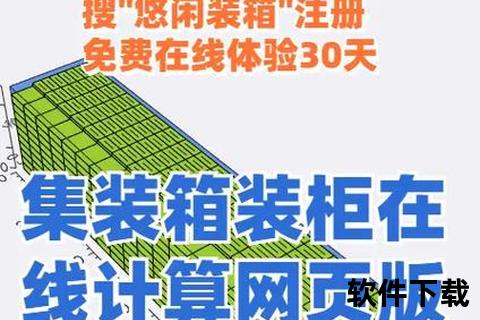
2024年青岛港的拥堵事件曾导致37%的集装箱被迫临时改配,传统预装方案完全失效。而采用智能装箱系统的企业,通过实时对接港口作业数据,在48小时内完成全部368个集装箱的配载重构,空间利用率仍保持91%以上。
高效能智能集装箱装箱计算软件轻松优化空间利用率新体验的独特价值,在于其构建的“数字孪生”系统。该系统可同步集装箱定位传感器、货物温湿度检测仪等物联网设备数据。如某冷链物流企业通过实时监测货物状态,在运输途中动态调整14个冷藏箱的货物分布,使制冷能耗降低22%。
行业数据显示,具备实时调整功能的软件可使突发状况处理效率提升4.3倍。某汽车零部件供应商的实践更具说服力——当紧急订单导致装载货物增加23%时,系统通过货物压缩算法和托盘重组技术,在原有集装箱数量内完成装载,避免额外租用12个集装箱产生的费用。
三、复杂场景能否实现普适性应用?
在新能源运输领域,锂电池集装箱的防爆间距要求导致传统装载率不足65%。某龙头企业采用智能软件的“安全阈值建模”功能,通过三维静电分布模拟和防撞缓冲区优化,将装载密度提升至82%,同时完全符合UN38.3国际标准。
高效能智能集装箱装箱计算软件轻松优化空间利用率新体验正在突破行业边界。家居行业的“魔方装载”案例尤为典型:某宜家供应商利用软件的柔性变形算法,对2,346种异形家具进行共形压缩计算,使标准集装箱容纳量增加41%。更通过AR装箱指导系统,将工人操作失误率从15%降至3%。
该技术甚至延伸至建筑领域。某模块化建筑公司将集装箱房运输效率提升270%——软件将墙体、框架等构件转化为可嵌套的“俄罗斯方块”模型,通过拓扑优化算法实现98.7%的空间填充率,相比传统运输方式,单项目节省运费超80万元。
可操作建议:
1. 优先选择具备混合算法的系统,如同时支持启发式算法和精确算法的平台,应对不同复杂度场景
2. 验证系统的实时对接能力,要求供应商演示与WMS、TMS等系统的数据贯通,确保动态调整可行性
3. 关注可视化交互设计,选择支持3D模拟、AR指导的系统降低操作门槛,如某企业通过可视化界面使培训时间缩短76%
4. 实施分阶段验证,建议先用免费试用版处理10-20个典型集装箱,对比人工方案的改进空间
通过高效能智能集装箱装箱计算软件轻松优化空间利用率新体验,物流行业正在经历从经验驱动到数据驱动的范式变革。当算法开始理解货物的“语言”,集装箱空间的每一次呼吸都将转化为真金白银的效益。