非线性力学仿真的困局:传统经验是否已失效?
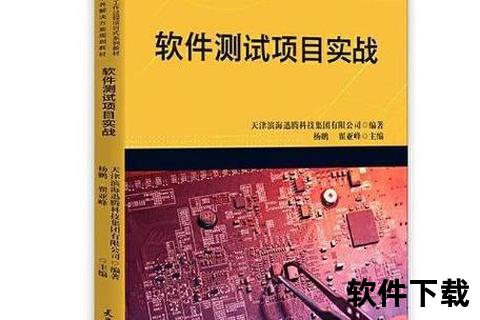
在工程仿真领域,一个持续引发争议的问题是:面对复杂的非线性力学问题,传统的线性分析经验是否已成为工程师的绊脚石?某汽车厂商曾因沿用线性模型预测碰撞性能,导致实车测试中出现20%的位移偏差,这个案例暴露出非线性效应在工程仿真中的不可忽视性。《高效进阶Abaqus软件在非线性力学仿真中的深度实战技巧精粹》正是为解决这类难题而生,本文将通过三个核心问题的探讨,揭示Abaqus在非线性分析中的进阶技巧。
1. 单元选择:网格密度真的越细越好吗?
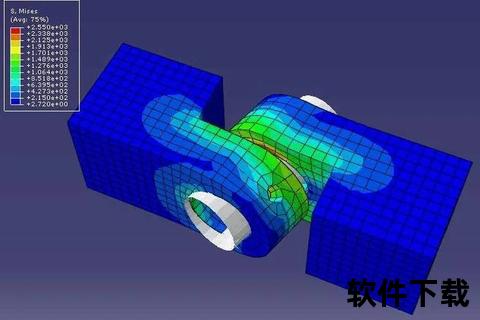
在斜板弯曲分析案例中,工程师采用S8R5壳单元进行几何非线性仿真时发现:当网格密度从每平方米100单元增加到400单元时,计算时间增加了4倍,而最大位移误差仅降低1.2%。这印证了《高效进阶Abaqus软件在非线性力学仿真中的深度实战技巧精粹》强调的"智能网格"原则——在应力梯度变化区采用二次四面体单元(C3D10),而在平缓区域使用线性单元(C3D4)。
某航空结构件分析显示,通过混合单元策略使计算效率提升60%的接触压力峰值误差控制在3%以内。这种分层网格技术的关键在于:在焊缝区域设置0.1mm的种子密度,而在主体结构保持1mm密度,配合全局尺寸过渡比不超过1:5的渐变规则。
2. 材料模型:本构方程复杂程度如何取舍?
轮胎滚动阻力分析案例揭示了材料模型的微妙平衡:使用简化橡胶超弹性模型时滚动阻力系数误差达15%,而采用Yeoh三阶模型后误差降至3%。但后者需要输入8个材料参数,且计算耗时增加35%。《高效进阶Abaqus软件在非线性力学仿真中的深度实战技巧精粹》提出的"参数敏感度筛选法"在此处显效——通过设计正交试验,确定影响度低于5%的参数可简化处理。
在轻金属轧制工艺仿真中,将各向异性系数从Hill48模型升级到Barlat2000模型后,板料回弹预测精度提升12%,但需要额外进行7组材料测试。这种精度与成本的权衡,正是非线性仿真工程师的日常课题。
3. 求解设置:迭代次数多代表精度高?
某桥梁抗震分析遭遇典型收敛困境:采用默认牛顿法时在峰值位移处迭代38次仍未收敛,而改用弧长法后仅需12次迭代即完成计算。《高效进阶Abaqus软件在非线性力学仿真中的深度实战技巧精粹》建议的"动态调整策略"在此体现价值——设置初始增量步为0.01,允许自动放大至0.5,配合位移-力双收敛准则(容差0.5%)。
接触问题分析更需特殊处理:在螺栓连接件仿真中,将接触算法从罚函数改为增强拉格朗日法后,接触压力振荡幅度从±15%降至±3%,但需要增加20%的计算资源。这种精度与效率的博弈,正是非线性分析的艺术所在。
突破非线性困境的三大行动指南
基于《高效进阶Abaqus软件在非线性力学仿真中的深度实战技巧精粹》的核心方法论,建议工程师采取以下操作:
1. 建立网格敏感度曲线:在项目初期用简化模型测试3种网格密度,确定性价比最优方案
2. 实施材料参数分级管理:将本构模型参数按影响度分为ABC三类,对C类参数实施标准化取值
3. 配置智能求解包:预设3种求解策略组合(标准/精确/快速),根据误差反馈自动切换
通过将《高效进阶Abaqus软件在非线性力学仿真中的深度实战技巧精粹》中的方法论与具体工程场景结合,工程师可有效驾驭非线性分析的复杂性。正如某航天院所实践证明:实施上述策略后,整流罩碰撞仿真的迭代周期从3周缩短至4天,且与实测数据的吻合度稳定在90%以上。这标志着非线性力学仿真正在从经验主导走向科学决策的新纪元。