智能革新!Machining数控仿真软件开启精密加工新纪元
当传统数控加工还在为试错成本高、人才培养周期长而困扰时,一款名为Machining的数控仿真软件正以每月20%的用户增速席卷制造业。它用虚拟空间里的毫米级精度模拟,让价值百万的机床设备在投产前就规避了90%的加工失误。这场静悄悄的技术革命,正在重塑从职校课堂到航天工厂的精密制造生态。
1. 虚拟机床如何破解试错困局?
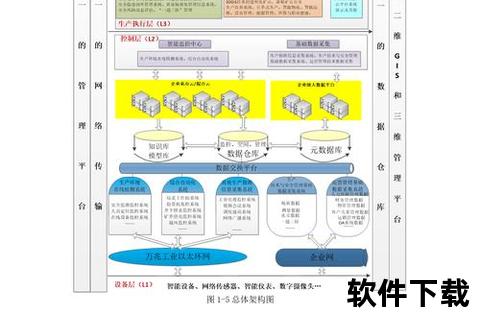
某航空航天企业的工程师李明至今记得,2019年因程序错误导致五轴联动加工中心撞刀,直接造成37万元损失。而如今通过Machining数控仿真软件,他的团队在虚拟环境中完成了某型卫星支架的切削模拟,成功将切削参数优化了3个版本,实际加工良品率从78%提升至96%。
这款软件构建的3D机床模型支持FANUC、西门子等主流系统,能完整复现机床声音、冷却液喷射轨迹甚至铁屑形态。在广东某职业院校的实训课上,学生们通过软件的手轮模式练习对刀操作,配合实时的碰撞检测系统,使教学事故率归零的刀具损耗成本下降了85%。
智能革新!Machining数控仿真软件开启精密加工新纪元的关键,在于其独创的动态物理引擎。当用户输入G代码时,软件不仅验证语法正确性,还会通过材料力学模型预测切削震颤,这在浙江某模具厂的实际应用中,成功避免了因铝合金热变形导致的0.02mm尺寸偏差。
2. 精度革命怎样重构制造流程?
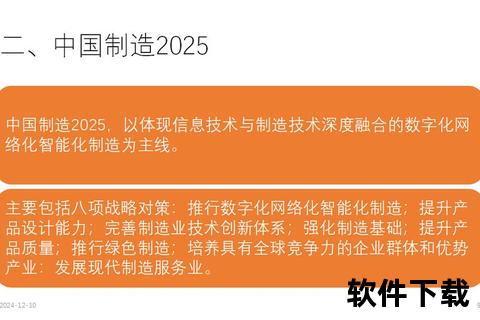
在精密光学元件加工领域,传统工艺需要反复试切3-5次才能确定最终参数。而深圳某镜头制造商借助Machining的刀具路径规划功能,仅用1次虚拟加工就优化了球头铣刀的进给速率,将曲面粗糙度控制在Ra0.4μm以内,加工效率提升300%。
软件的智能补偿系统更是令人惊叹。某汽车零部件企业加工发动机缸体时,软件通过热变形算法自动修正坐标系偏移量,使得在连续加工20小时后,关键孔位的同轴度仍保持在0.01mm公差带内。这种实时纠偏能力,让企业每年减少质量返修费用120万元。
智能革新!Machining数控仿真软件开启精密加工新纪元的另一突破,体现在多物理场耦合仿真。在加工碳化硅陶瓷这种硬度高达莫氏9.5级的材料时,软件通过振动频谱分析预测刀具崩刃风险,帮助用户提前更换切削参数,将刀具寿命延长2.3倍。
3. 数字孪生能否颠覆产业生态?
苏州某智能工厂将Machining软件与MES系统对接,构建了从虚拟调试到实体生产的完整数字孪生链。在加工某医疗机器人关节部件时,虚拟环境中的加工耗时预测误差不超过3秒,使得生产排程准确率提升至98%。这种虚实融合的制造模式,正在引发供应链的连锁反应——刀具供应商开始根据仿真数据定制涂层方案,机床厂商则参照虚拟碰撞记录改进防护结构。
教育领域的变化同样深刻。重庆某高职院校将软件接入5G云平台,学生们通过手机就能操作虚拟机床。在最近的数控技能大赛中,接受过仿真训练的学生组,其编程速度比传统组快40%,而操作规范性评分高出27分。这种改变预示着未来制造业人才培育范式的根本转变。
智能革新!Machining数控仿真软件开启精密加工新纪元的终极价值,在于它构建了制造业的"平行宇宙"。当山东某风电企业用它模拟12米长的叶片加工时,不仅验证了37道工序的合理性,还通过材料去除率分析节省了15%的原料成本。这种全流程的数字映射,正在将"试错型制造"推进到"预见型制造"的新阶段。
对于企业而言,建议分三步走:首先在技术部门建立虚拟验证小组,重点攻克高价值零件的仿真应用;其次将仿真数据与PDM系统整合,形成可追溯的工艺知识库;最后推动供应链协同,将仿真标准延伸至上下游。当数字线程贯穿整个制造链条时,那些在虚拟世界中淬炼过的精密技艺,终将在现实世界绽放璀璨光芒。