当传统工业遭遇智能革命,谁在定义中控软件的未来?
在山西某大型煤矿的控制中心里,操作员老张紧盯着屏幕上的数据曲线,突然发现某个关键参数异常。十年前,他需要手动翻阅三本操作手册,耗时半小时才能找到故障点;如今,系统自动弹出了三维可视化定位图,并推荐了三种处理方案——这种变化背后,正是中控软件智能管控系统带来的革命性突破。在这场工业智能化浪潮中,"智慧赋能未来 全方位升级中控软件智能管控新标杆"正引发行业深刻变革:究竟怎样的控制系统才能满足智能制造时代的复杂需求?
一、基础架构能否实现全场景互联互通?
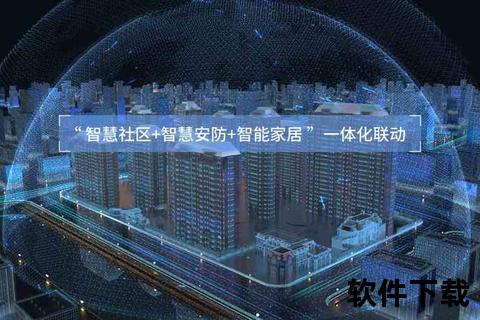
传统DCS系统常被诟病为"信息孤岛",就像某化工企业曾面临的困境:15个生产装置的数据分散在8套独立系统,每次工艺调整需要协调三个部门。中控技术推出的i-OMC系统给出了创新答案——通过"工厂操作系统+工业APP"架构,构建起覆盖设备、工艺、数据的统一数字基座。在鹏飞集团智能选煤厂项目中,这套系统将重介密度控制误差从±0.03g/cm³压缩至±0.005g/cm³,精煤回收率提升2.3%,年增收超2000万元。
该系统的突破性在于"E网到底"设计,融合5G、APL等12种传输协议,让山西永红煤业的120万吨选煤生产线实现了从PLC到云端的毫秒级响应。这种全连接能力,使某氯碱企业成功将定员从150人缩减至30人,同时设备故障预警准确率达到98%。
二、数据驱动能否真正解放生产力?
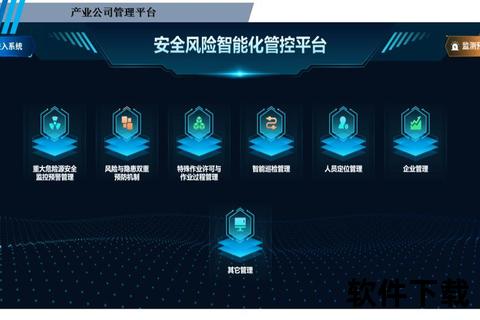
广东某LNG接收站曾因人工操作导致每年2000万元的能源损耗,引入中控时序大模型TPT后,通过自主监督优化算法,将卸船作业时间缩短15%,罐存波动幅度降低60%。这种基于45亿条工业时序数据训练出的AI模型,能像经验丰富的工程师一样预判设备状态,在万华化学的智能工厂中,设备自主诊断准确率已达92%。
更令人惊叹的是浙江某乙二醇工厂的案例:通过AI驱动的回路自整定技术,原本需要3名工程师耗时一周调试的PID参数,现在系统可自动完成并持续优化。这使得该厂自控率从75%跃升至99%,操作频次下降90%,相当于每年解放2000人工时。这种变革印证了"智慧赋能未来 全方位升级中控软件智能管控新标杆"的核心价值——将人类从重复劳动中解放,专注于价值创造。
三、生态共建能否打破行业壁垒?
在国家管网集团的智慧能源决策系统中,中控软件与12家设备厂商、5家算法公司共建的开放平台,让3000公里输油管道的能耗降低2.2%,相当于每年节省3.6万吨标准煤。这种生态化发展模式,在EGYPES国际能源展上得到验证:中控UCS通用控制系统支持89种工业协议,可无缝对接西门子、ABB等国际品牌设备,帮助埃及某炼油厂缩短50%系统集成周期。
在深圳某智能工厂,基于中控PA+BA架构构建的"数字孪生体",实现了从生产排程到设备维护的全链条协同。通过与物流企业数据互通,原料库存周转率提升40%,紧急订单响应时间从72小时压缩至8小时。这些案例揭示着"智慧赋能未来 全方位升级中控软件智能管控新标杆"的深层逻辑——独木难成林,生态共赢才是智能制造的未来。
破局之路:三步构建智能管控体系
对于寻求转型的企业,建议分阶段实施:首先建立统一数据中台,打通设备层到管理层的数字通道;其次部署智能算法模块,从关键工序切入实现局部优化;最后构建开放应用生态,引入合作伙伴共建解决方案。正如某汽车零部件厂商的经验:通过中控InPlant SCADA系统搭建基础平台后,逐步接入AI优化模块,三年内将综合运营效率提升37%。
在这场工业智能革命中,"智慧赋能未来 全方位升级中控软件智能管控新标杆"不仅是技术升级,更是生产关系的重构。当控制系统从"机械手臂"进化为"工业大脑",我们看到的不仅是效率提升的数字奇迹,更是人类智慧与机器智能协同共生的未来图景。或许正如德国工业4.0专家施耐德所言:"真正的智能制造,始于数据流动,成于系统共生。