钣金制造的“生死局”:智能化是唯一出路吗?
在机械制造领域,钣金加工曾长期被视为“苦力活”——工人围着笨重的机床打转,图纸堆叠如山,订单稍有变动就要全员返工。某钣金厂老板曾吐槽:“客户今天要改个圆角,明天要加个孔位,光图纸确认就要耗三天,利润全砸在沟通成本里了。”这种传统模式不仅效率低下,还面临人工成本飙升、利润率跌破5%的困境。
随着工业4.0浪潮席卷,一批创新智能钣金软件正悄然改变这一局面。它们从设计、排产到生产全流程切入,让精密制造的每个环节都“会思考”。创新智能钣金软件高效赋能精密制造全流程升级,究竟如何实现?我们从三个关键问题切入。
1. 传统钣金工艺如何突破效率瓶颈?
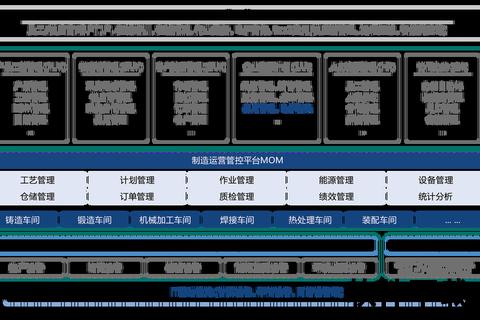
以江苏某金属制品厂为例,过去手工展开钣金件需要2小时,误差率高达15%。引入金林钣金展开软件后,只需输入参数,系统自动生成三维模型和展开图,并通过CAD接口直连激光切割机。原本复杂的折边计算、套料优化全部由算法完成,单件加工时间缩短至20分钟,材料利用率从65%提升至92%。
更颠覆性的是创新智能钣金软件高效赋能精密制造全流程升级的协同能力。亚威机床开发的MES系统,将ERP订单一键导入生产端。某空调外壳订单突发设计变更,系统10分钟内完成新图纸解析、工艺路线调整和物料调配,避免了过去因信息滞后导致的3天停工。这种“动态响应”模式,让企业紧急插单处理效率提升40%。
2. 复杂订单如何实现柔性化生产?
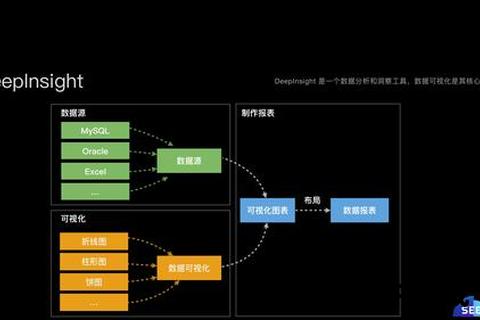
面对“小批量、多品种”的市场需求,捷匠网络科技的工业互联网平台给出答案。某电梯部件制造商通过平台接入后,实现了“云端接单-智能拆单-分布式生产”的链路。例如一批定制化控制柜订单被拆解为56个零件,由3家协作厂同步加工,再通过AGV自动匹配组装。全程数据可视,交付周期从28天压缩至9天,库存周转率提升3倍。
另一典型案例是伟泰科技的离散型智能制造系统。其独创的“模拟配料”功能(见图1),可在5分钟内计算出插单对现有排产计划的影响,并给出最优物料调配方案。这套系统帮助某医疗器械企业将设备综合利用率从68%提升至89%,订单准时交付率突破98%。这正是创新智能钣金软件高效赋能精密制造全流程升级的直观体现。
3. 全流程协同如何打通信息孤岛?
传统钣金厂最头疼的问题莫过于“数据断链”——设计部门用CAD,生产部门看纸质工单,仓库还在用Excel记账。某汽车零部件企业为此付出惨痛代价:因BOM表未及时更新,导致200件钣金件因孔位偏差报废,直接损失超80万元。
而通过创新智能钣金软件高效赋能精密制造全流程升级,亚威机床的PLM(产品生命周期管理)系统将设计、工艺、制造数据无缝串联。某新能源电池箱体项目从3D建模到首件下线仅用72小时,关键环节数据自动校验,设计变更响应速度提升6倍。更值得关注的是设备健康管理系统:通过在折弯机丝杠安装振动传感器,结合机器学习算法,可提前48小时预警设备故障,维护成本降低35%。
破局之道:三步走策略
对于亟待转型的钣金企业,建议从三个维度切入:
1. 优先引入轻量化软件工具:如金林展开软件,初期投入约5万元即可解决80%的图纸处理痛点;
2. 构建协同平台消除数据壁垒:选择支持ERP/MES/CAD联动的系统,重点打通订单-设计-生产链路;
3. 培养“数字工匠”团队:某企业通过“软件实操+产线轮岗”培训,6个月内将员工数字化技能匹配率从23%提升至81%。
这场钣金制造的智能化革命,不是选择题而是生存题。正如某行业观察者所言:“未来十年,不会用数据‘说话’的钣金厂,可能连‘说话’的机会都没有。”
--