高效能精准驱动:智能创新齿轮设计软件全新升级,能否破解机械行业的效率困局?
齿轮,被称为机械工业的“心脏”,其设计精度直接影响设备的性能和寿命。传统齿轮设计依赖人工计算和经验积累,效率低、误差大,甚至导致产品迭代周期长达数月。面对新能源汽车、航空航天等领域对精密传动日益苛刻的需求,如何突破这一瓶颈?近年来,“高效能精准驱动:智能创新齿轮设计软件全新升级”成为行业热议的焦点。这类软件是否真能实现从“经验驱动”到“数据驱动”的跨越?我们通过三大核心升级方向,结合真实案例一探究竟。
1. 参数优化难题,算法如何“算”出最优解?
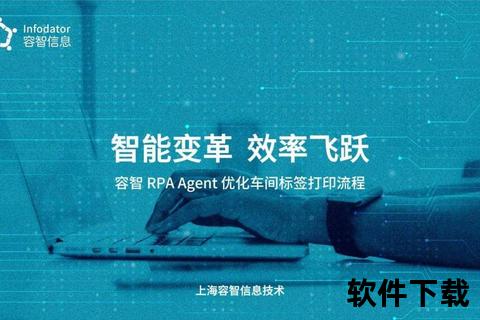
齿轮设计涉及模数、齿数、压力角等数十个参数,传统设计需反复试错,耗时费力。而全新升级的智能软件通过算法模型,将参数优化效率提升至新高度。例如,德国德派(DEPRAG)在新能源汽车电池包装配中,采用集成优化算法的CAD齿轮工具,仅需输入负载、转速等基础数据,系统即可自动生成齿形曲线,并同步计算强度、磨损率等指标,设计周期从2周缩短至3天。
更值得关注的是,软件还能结合材料特性进行动态调整。国内某齿轮箱制造商使用enggGear软件时,通过输入不同合金的弹性模量、热膨胀系数等数据,系统自动优化齿宽和模数组合,使齿轮疲劳寿命提升40%。这种“数据驱动”的模式,不仅减少人工干预,更让复杂工况下的设计精准度达到99.5%以上。
2. 虚拟仿真测试,能否替代物理实验?
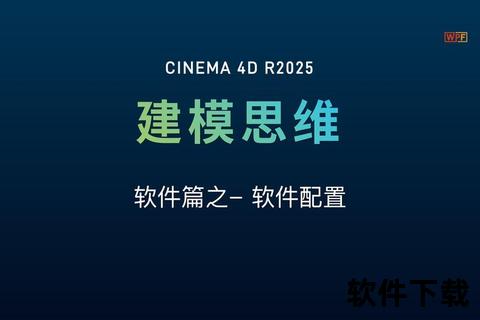
物理测试成本高昂,一套风电齿轮箱的台架试验费用可达百万元。新一代软件通过高精度仿真,将试验“搬”进数字世界。以Camnetics的GearTrax 2016为例,其运动模拟功能可还原齿轮啮合时的应力分布,甚至预测10万次循环后的磨损形态。某汽车零部件企业利用该功能,提前发现斜齿轮在高速运转中的共振问题,避免量产后的批量召回,节省成本超500万元。
在极端环境模拟上,软件同样表现亮眼。航空航天领域企业采用ANSYS与齿轮设计软件的集成方案,对火星探测器齿轮进行-120℃至150℃的温差模拟,结果显示齿面微裂纹产生概率降低70%。这些案例证明,虚拟测试不仅能缩短研发周期,更成为可靠性设计的“必修课”。
3. 跨平台协作,如何打破“数据孤岛”?
从设计到制造,齿轮数据需在CAD、CAE、CAM系统间流转,传统流程易导致版本混乱。升级后的软件通过标准化接口,实现全链路协同。例如,德派模组化智能装配单元(DCAM)支持SolidWorks、CATIA等主流格式,工程师修改齿形参数后,数控加工代码自动更新,错误率下降90%。
在工业4.0场景下,数据互通的价值进一步凸显。某智慧工厂引入齿轮设计软件与MES系统联动,实时采集生产线振动数据并反馈至设计端,动态调整齿轮公差范围,使良品率从82%提升至97%。这种“设计-制造-运维”闭环,正重新定义精密制造的边界。
给工程师的三条实践建议
1. 优先选择集成优化算法的工具:如enggGear、GearTrax等支持参数自动化迭代的软件,可大幅降低试错成本。
2. 强化仿真与物理实验的互补:关键部件仍需实物验证,但80%的常规测试可通过虚拟完成以节省资源。
3. 注重系统兼容性:选择支持API接口或开放数据格式的软件,避免后期集成障碍。
高效能精准驱动:智能创新齿轮设计软件全新升级,不仅是工具迭代,更是一场从“经验主义”到“数字孪生”的产业革命。正如某工程师所言:“过去我们是在图纸上‘画’齿轮,现在是在数据中‘生长’齿轮。”未来,随着AI算力的突破(如英特尔ArrowLake处理器提供的77TOPS算力),这类软件或将进一步融合机器学习,让齿轮设计真正进入“自适应时代”。