当传统制造业遭遇效率瓶颈,仿真技术能否成为破局关键?
在工业4.0浪潮席卷全球的今天,制造业对“高精度、高效率、低成本”的追求愈发迫切。传统CNC(计算机数控)加工面临诸多痛点:编程试错成本高、设备闲置浪费产能、人工培训周期长……这些问题如同无形的锁链,束缚着智能精工的升级步伐。极致逼真CNC仿真软件赋能智能精工高效革新新时代的技术应运而生。它不仅通过虚拟环境模拟真实加工场景,更以数据驱动的方式优化生产全流程,成为推动制造业转型的“数字引擎”。
1. 仿真软件如何破解“试错成本高”的行业难题?
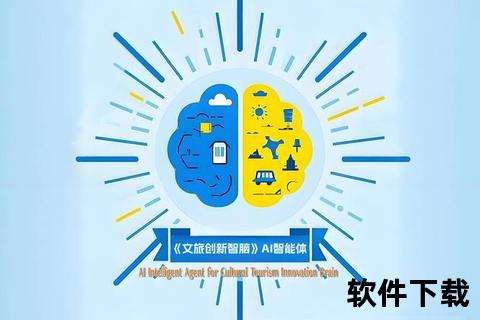
在传统CNC加工中,一个编程错误可能导致刀具断裂、材料报废甚至设备损坏。以某轨道交通零部件企业为例,其螺栓螺母生产线曾因工艺参数设置不当,导致良品率长期低于80%,每年损失超千万元。而引入德国凯勒CNC仿真软件后,该企业通过三维动态模拟技术,在虚拟环境中验证加工路径和刀具轨迹,提前规避了90%以上的编程错误。
更值得一提的是,海天精工在智能制造升级中,通过三维工艺仿真软件将新产品研发周期缩短30%以上。这种“先模拟、后生产”的模式,不仅减少了物理试错成本,还让工程师能够快速迭代优化方案。例如,某汽车零部件厂商利用仿真软件的自动代码生成功能,将复杂曲面的加工编程时间从8小时压缩至30分钟。
2. 虚拟机床如何实现“设备利用率翻倍”?
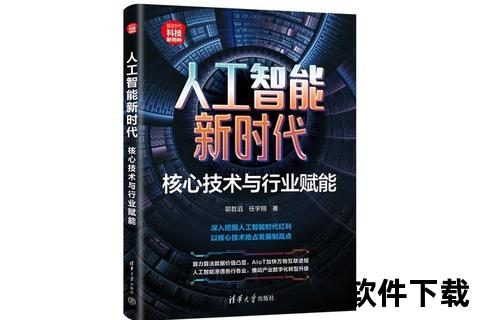
据统计,国内CNC设备平均利用率不足60%,部分企业甚至低于40%。造成这种现象的核心原因在于生产调度不科学和程序调试耗时。而极致逼真的CNC仿真软件,通过构建数字孪生系统,让企业能够在虚拟环境中完成以下突破:
智能排产优化:宁波某模具厂应用SymPlus仿真软件的动态虚拟车间功能,将设备利用率从58%提升至82%。系统通过模拟不同订单组合的加工耗时,自动推荐最优排产方案。
刀具寿命管理:精工智能工厂改造案例显示,通过仿真软件对刀具磨损的预测分析,刀具更换周期延长20%,年节省耗材费用超百万元。
无人化生产验证:某航空企业利用PowerMill的投影范围控制功能,在虚拟环境中完成5轴联动加工验证,使高端机床的夜间无人值守运行成为可能。
3. 数字孪生技术怎样重塑人才培养体系?
制造业面临“老师傅退休、新技工断层”的困境。传统CNC操作培训需占用实体设备,每人次培训成本高达万元。而仿真软件通过以下方式颠覆传统:
沉浸式教学:德国凯勒软件的多媒体模拟模块,以3D动画分解机床结构原理,使学员对G代码指令的理解效率提升3倍。
故障模拟训练:某职业院校引入虚拟车间系统后,学员可在安全环境中模拟应对刀具崩刃、材料变形等30余种突发状况,实操合格率从65%跃升至92%。
远程协作升级:上海某企业通过IoT平台接入仿真系统,实现多地工程师同步调试加工程序,项目交付周期缩短40%。
从虚拟到现实:企业该如何迈出关键一步?
极致逼真CNC仿真软件赋能智能精工高效革新新时代的趋势已不可逆转。对于企业而言,落地实施需分三步走:
1. 诊断痛点,分阶段投入
中小型企业可优先选择模块化仿真工具(如PowerMill的2D铣削模块),针对具体工艺痛点试点应用,避免盲目追求“大而全”的系统。
2. 数据贯通,构建数字闭环
参考海天精工的MES+仿真集成模式,将虚拟验证数据与生产执行系统打通,实现工艺参数自动优化迭代。
3. 人才转型,培养“双栖工程师”
建立“仿真操作+实体加工”的复合培训体系,如某车企要求技术员必须通过SymPlus软件的IHK认证考试,方可操作高端机床。
在这场制造业的数字化革命中,仿真软件不仅是成本控制的利器,更是打开智能制造大门的钥匙。正如精工智能工厂的实践所证:当虚拟与现实深度融合时,生产效率的边界将被不断突破,极致逼真CNC仿真软件赋能智能精工高效革新新时代的蓝图正在成为现实。