当精密加工遭遇瓶颈,技术革新能否打破困局?
在精密制造领域,一个长期争议的问题始终存在:传统数控加工是否已触及技术天花板?以航空发动机叶片为例,其复杂曲面加工误差需控制在0.005毫米以内,但传统仿真软件仅能模拟单工序场景,导致实际生产中出现刀具碰撞、参数偏差等问题,返工率高达15%。这一矛盾在微型医疗器械、精密模具等对空间和精度要求更严苛的领域尤为突出。
而近年来,「沉浸式智能数控模拟仿真软件全方位提升精密加工新境界」的技术突破,正以虚实融合的方式重构制造流程。这种技术不仅将机床、工件、刀具的动态数据实时映射到三维空间,更通过人工智能算法预判风险,为精密加工开辟全新可能。
1. 精度提升:虚拟空间如何突破物理限制?
在航天领域某型号卫星支架加工中,传统方法因无法模拟微米级振动对刀具路径的影响,导致首批次产品合格率仅为72%。引入沉浸式仿真系统后,工程师通过虚实联动的「动态误差补偿模块」,将刀具轨迹与机床振动数据实时关联。系统自动生成的补偿方案使加工精度提升至99.8%,材料损耗降低40%。
该软件的核心突破在于其「超分辨率建模技术」,能将直径0.1毫米的微型铣刀运动轨迹放大500倍可视化。例如深圳某精密模具企业使用该功能后,成功解决了微型齿轮箱加工中的刀具崩刃问题,单件加工时间从45分钟缩短至28分钟。
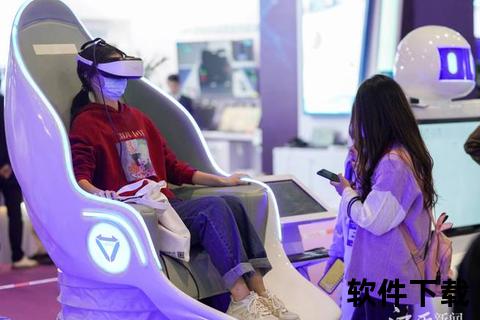
2. 协同优化:多工序如何实现无缝衔接?
汽车变速箱壳体加工涉及27道工序,传统模式下各环节数据孤立,曾导致某车企因热处理工序参数未及时同步,造成整批零件硬度超标。沉浸式系统通过「全链路数字孪生」功能,将冲压、切削、热处理等工序数据整合至统一平台。
典型案例显示,某企业应用该技术后:
工序协同效率提升60%,换模时间从3小时压缩至45分钟
通过「智能纠偏算法」提前15分钟预警刀具磨损风险
产线整体OEE(设备综合效率)从68%跃升至89%
这种变革源于软件对ISO14649标准数据的深度解析能力,可将加工代码自动转化为三维动态模型,实现从CAM编程到实际生产的全流程验证。
3. 人才培育:技术门槛能否被智能化解构?
苏州某职业技术学院的教学实验揭示:传统数控教学需6个月培养基础操作技能,而通过沉浸式系统的「AR辅助教学模块」,学员可在虚拟机床中反复练习高危操作。数据显示:
刀具参数设置错误率从35%降至8%
复杂曲面编程学习周期缩短50%
学生参与企业实际项目比例从12%提升至47%
软件内置的「智能导师系统」更具革新意义。当学员操作数控面板时,系统会通过眼球追踪技术判断其注意力焦点,实时推送相关参数说明。这种「场景化知识供给」模式,让某工具制造企业的员工培训效率提升3倍。
迈向智能制造的三个行动指南
1. 引入动态学习算法:选择支持机器学习迭代的软件,如某头部系统可基于历史数据自动优化切削参数库,使加工效率每季度提升2%-5%
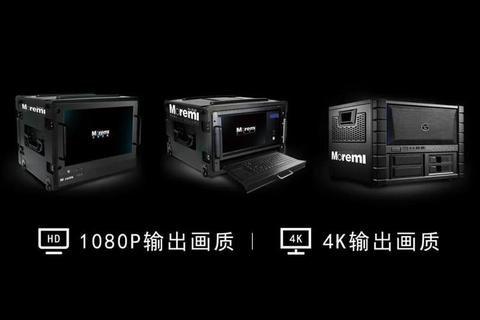
2. 构建跨平台数据池:通过OPC-UA协议打通仿真软件与MES、ERP系统,某精密零件厂商借此实现从设计到交付的全流程周期压缩28%
3. 建立虚实联动机制:建议企业配置1:10的虚拟机床资源池,某汽车零部件工厂通过该方案,将新工艺验证成本从单次5万元降至8000元
这场由「沉浸式智能数控模拟仿真软件全方位提升精密加工新境界」引发的技术革命,正在重塑精密制造的DNA。当虚拟空间的每一次刀具路径优化都能转化为现实世界的效率跃升,当三维模型中的每个数据点都在为实际生产提供决策支撑,我们或许正在见证精密加工从「经验驱动」到「数据驱动」的历史性跨越。